Trainings
Our training services in Kenya encompass a wide range of topics tailored to meet the specific needs of organizations and individuals across various industries. We offer interactive and engaging training programs delivered by experienced professionals to enhance knowledge, skills, and competencies in areas such as:
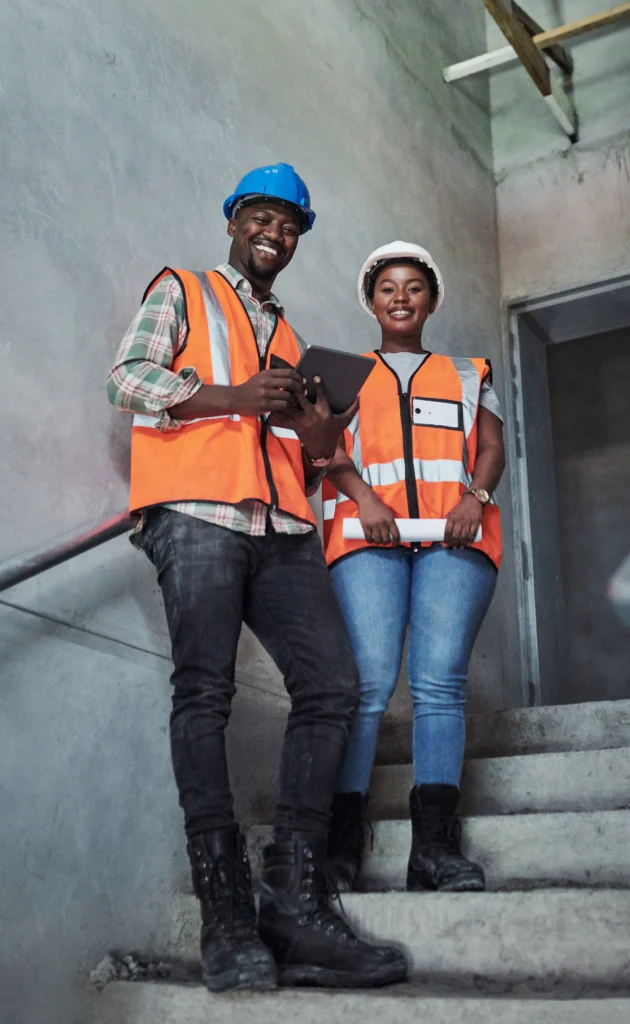
Our Trainings
Our workplace safety training programs in Kenya cover essential topics such as First Aid, Fire Safety, and Occupational Safety and Health (OSH), ensuring that organizations and individuals are equipped with the knowledge and skills to create a safe and healthy work environment. Here’s an overview of each training:
1. First Aid Training: Our First Aid training equips participants with life-saving skills and knowledge to provide immediate assistance in medical emergencies. Topics include CPR (Cardiopulmonary Resuscitation), wound care, fracture management, choking relief, and emergency response protocols. Participants learn how to assess situations, administer first aid treatments, and effectively communicate with emergency services.
2. Fire Safety Training: Our Fire Safety training educates participants on fire prevention, evacuation procedures, and proper use of fire extinguishers and other firefighting equipment. Topics include fire detection, fire hazards identification, emergency evacuation plans, fire suppression techniques, and post-fire procedures. Participants learn how to respond effectively to fire emergencies, minimize risks, and protect lives and property.
3. Occupational Safety and Health (OSH) Training: Our OSH training focuses on promoting safe work practices and preventing workplace injuries and illnesses. Topics include hazard identification, risk assessment, personal protective equipment (PPE) usage, ergonomics, chemical safety, electrical safety, and machine guarding. Participants learn how to recognize and mitigate workplace hazards, comply with OSH regulations, and foster a culture of safety in the workplace.
Our training programs are interactive, engaging, and conducted by experienced instructors with expertise in their respective fields. We offer flexible training formats, including classroom sessions, hands-on demonstrations, simulations, and online modules, to accommodate the needs and preferences of participants. By investing in workplace safety training, organizations demonstrate their commitment to protecting their employees, reducing accidents and injuries, and promoting a culture of safety and well-being.
Our Work at Height, Scaffolding, and Rope Access training programs in Kenya are designed to equip participants with the knowledge and skills necessary to perform tasks safely and effectively in elevated environments. Here’s an overview of each training:
1. Work at Height Training: Our Work at Height training focuses on identifying hazards associated with working at elevated levels and implementing controls to mitigate risks. Participants learn about fall protection systems, including personal fall arrest systems (PFAS), guardrails, and safety nets. Topics include risk assessment, ladder safety, scaffolding, working on roofs, and emergency response procedures. The training emphasizes the importance of planning, proper equipment usage, and adherence to safety regulations to prevent falls and accidents.
2. Scaffolding Training: Our Scaffolding training provides participants with comprehensive knowledge of scaffolding systems, components, assembly, and inspection procedures. Participants learn how to erect, dismantle, and inspect scaffolds safely, ensuring stability and structural integrity. Topics include scaffold types (e.g., supported scaffolds, suspended scaffolds), scaffold hazards, load capacities, fall protection measures, and regulatory requirements. The training covers best practices for scaffold erection, maintenance, and usage to prevent accidents and ensure a secure working platform.
3. Rope Access Training: Our Rope Access training equips participants with the skills needed to perform work tasks in challenging environments using rope access techniques. Participants learn rope rigging, anchor systems, descent, ascent, and rescue procedures. Topics include rope access equipment usage, safety protocols, communication techniques, and emergency response planning. The training emphasizes risk management, teamwork, and adherence to industry standards (e.g., IRATA, SPRAT) to ensure safe and efficient operations at height.
Our training programs combine theoretical knowledge with practical exercises and hands-on demonstrations to enhance participant learning and retention. Certified instructors with extensive experience in work at height, scaffolding, and rope access deliver the training, ensuring high-quality instruction and compliance with industry standards. By investing in these training programs, organizations demonstrate their commitment to worker safety, compliance with regulations, and prevention of accidents and injuries in elevated work environments.
Our Scissor Lift Training program in Kenya provides comprehensive instruction on the safe operation and maintenance of scissor lifts, ensuring that participants have the knowledge and skills necessary to work confidently and effectively with this equipment. Here’s an overview of the training:
1. Equipment Familiarization: Participants learn about the various components and controls of scissor lifts, including platform controls, emergency stop mechanisms, hydraulic systems, and safety features. They gain an understanding of the different types of scissor lifts and their specific applications.
2. Safe Operation Practices: The training covers safe operating procedures for scissor lifts, including pre-operation inspections, proper positioning and leveling, safe ascent and descent, maneuvering in confined spaces, and working at height. Participants learn how to identify and avoid hazards such as overhead obstructions, uneven terrain, electrical hazards, and fall risks.
3. Fall Protection and Personal Safety: Participants learn about the importance of fall protection measures when working on scissor lifts, including the use of guardrails, personal fall arrest systems (PFAS), and restraint systems. They also receive instruction on wearing appropriate personal protective equipment (PPE) such as harnesses, hard hats, and safety footwear.
4. Emergency Procedures: The training covers emergency response procedures, including how to safely evacuate a scissor lift in the event of power failure or mechanical malfunction. Participants learn how to use emergency descent devices and rescue equipment, as well as how to communicate effectively during emergencies.
5. Maintenance and Inspections: Participants receive guidance on conducting routine maintenance tasks and pre-operation inspections to ensure that scissor lifts are in safe working condition. They learn how to identify and report equipment defects or deficiencies that could affect safety.
Our Scissor Lift Training program combines classroom instruction with hands-on practical exercises to reinforce learning and skill development. Certified instructors with expertise in scissor lift operations deliver the training, ensuring compliance with industry standards and regulations. By completing this training, participants gain the confidence and competence to operate scissor lifts safely, reducing the risk of accidents and injuries in the workplace.
Our Ladder Inspection Training program in Kenya provides comprehensive instruction on the proper inspection and maintenance of ladders to ensure they are safe for use in the workplace. Here’s an overview of the training:
1. Ladder Types and Components: Participants learn about different types of ladders commonly used in various industries, including step ladders, extension ladders, and platform ladders. They gain an understanding of ladder components, such as rungs, rails, feet, and safety features.
2. Inspection Procedures: The training covers detailed inspection procedures for ladders, including pre-use inspections, periodic inspections, and post-incident inspections. Participants learn how to visually inspect ladders for signs of damage, wear, corrosion, or defects that could compromise safety.
3. Common Defects and Hazards: Participants are trained to recognize common defects and hazards associated with ladders, such as bent or broken rungs, loose or missing hardware, damaged rails, and worn-out feet. They learn how to assess the severity of defects and determine whether a ladder is safe for use or requires repair or replacement.
4. Maintenance and Repair: Participants receive guidance on proper maintenance practices to keep ladders in good working condition, including cleaning, lubrication, and storage. They learn how to perform minor repairs and adjustments to address minor defects and ensure ladder safety.
5. Regulatory Compliance: The training covers relevant regulations and standards governing ladder safety, including OSHA regulations, ANSI standards, and industry best practices. Participants learn about their responsibilities as employers and employees to ensure compliance with safety regulations and prevent accidents and injuries.
6. Hands-On Exercises: The training includes hands-on exercises where participants practice inspecting ladders and identifying defects under the guidance of experienced instructors. This practical component reinforces learning and helps participants develop confidence in their inspection skills.
Our Ladder Inspection Training program is conducted by certified instructors with expertise in ladder safety and inspection. By completing this training, participants gain the knowledge and skills necessary to conduct thorough ladder inspections, identify potential hazards, and take appropriate corrective actions to prevent accidents and ensure a safe work environment.
Our Work Equipment Risk Assessment training program in Kenya provides participants with the knowledge and skills needed to conduct comprehensive risk assessments for various types of work equipment. Here’s an overview of the training:
1. Understanding Work Equipment: Participants learn about different types of work equipment commonly used in the workplace, including machinery, tools, vehicles, and lifting equipment. They gain an understanding of the hazards associated with each type of equipment and the potential risks to workers’ health and safety.
2. Risk Assessment Principles: The training covers the principles of risk assessment, including hazard identification, risk analysis, risk evaluation, and risk control measures. Participants learn how to systematically identify hazards associated with work equipment, assess the likelihood and severity of potential consequences, and prioritize risks for mitigation.
3. Risk Assessment Process: Participants are guided through the step-by-step process of conducting a work equipment risk assessment. They learn how to gather relevant information, assess hazards and risks, determine appropriate control measures, and document findings. Practical examples and case studies are used to illustrate key concepts and techniques.
4. Hazard Control Measures: Participants learn about various control measures that can be implemented to mitigate risks associated with work equipment. This includes engineering controls, administrative controls, and personal protective equipment (PPE). Emphasis is placed on the hierarchy of controls, with a focus on eliminating or minimizing hazards at the source.
5. Legal Requirements and Standards: The training covers relevant legal requirements and industry standards related to work equipment safety and risk assessment. Participants learn about their obligations under local regulations, such as the Occupational Safety and Health Act, as well as international standards, such as ISO 12100 and ISO 45001.
6. Practical Exercises: The training includes practical exercises where participants apply their knowledge and skills to conduct risk assessments for specific work equipment scenarios. This hands-on experience allows participants to practice identifying hazards, assessing risks, and developing control measures in a controlled environment.
Our Work Equipment Risk Assessment training program is delivered by experienced instructors with expertise in risk management and occupational safety. By completing this training, participants gain the confidence and competence to effectively assess risks associated with work equipment, implement appropriate control measures, and contribute to a safer work environment.
Our Hot Works Risk Assessment Training in Kenya equips participants with the knowledge and skills necessary to conduct thorough risk assessments for hot work activities, ensuring the safety of workers and the surrounding environment. Here’s an overview of the training:
1. Understanding Hot Work: Participants gain an understanding of what constitutes hot work, including activities such as welding, cutting, brazing, soldering, and grinding. They learn about the hazards associated with hot work, including fire, explosion, burns, and toxic fumes.
2. Regulatory Requirements: The training covers relevant regulations and standards governing hot work safety, including local occupational health and safety regulations, fire codes, and industry best practices. Participants learn about their legal obligations and responsibilities when performing hot work activities.
3. Risk Assessment Principles: Participants learn the principles of risk assessment as they apply to hot work activities. They learn how to systematically identify hazards, assess the likelihood and severity of potential consequences, and prioritize risks for mitigation. Emphasis is placed on the importance of proactive risk management to prevent accidents and injuries.
4. Hazard Identification: Participants learn how to identify common hazards associated with hot work activities, including flammable materials, combustible dusts, confined spaces, and nearby equipment or structures. They learn how to assess the risks posed by these hazards and determine appropriate control measures.
5. Control Measures: Participants learn about various control measures that can be implemented to mitigate risks associated with hot work activities. This includes implementing safe work procedures, providing appropriate personal protective equipment (PPE), using fire-resistant barriers and shields, and implementing fire prevention measures.
6. Hot Work Permit Systems: Participants learn about the importance of implementing a hot work permit system to control and monitor hot work activities. They learn about the key components of a hot work permit system, including permit issuance, pre-work inspections, fire watch requirements, and post-work checks.
7. Practical Exercises: The training includes practical exercises where participants apply their knowledge and skills to conduct hot work risk assessments for specific scenarios. This hands-on experience allows participants to practice hazard identification, risk assessment, and control measure selection in a controlled environment.
Our Hot Works Risk Assessment Training is conducted by experienced instructors with expertise in hot work safety and risk management. By completing this training, participants gain the confidence and competence to effectively assess risks associated with hot work activities, implement appropriate control measures, and ensure the safety of workers and the workplace.
Our Ergonomic Risk Areas and Prevention training program in Kenya focuses on identifying ergonomic hazards in the workplace and implementing strategies to prevent musculoskeletal disorders (MSDs) and other ergonomic-related injuries. Here’s an overview of the training:
1. Understanding Ergonomics: Participants learn about the principles of ergonomics and how they apply to the workplace. They gain an understanding of how ergonomic factors such as posture, repetitive motions, force exertion, and awkward positions can contribute to MSDs and other injuries.
2. Ergonomic Risk Assessment: The training covers the process of conducting ergonomic risk assessments to identify potential hazards in the workplace. Participants learn how to observe work tasks, identify ergonomic risk factors, assess their severity and frequency, and prioritize areas for intervention.
3. Common Ergonomic Risk Areas: Participants learn about common ergonomic risk areas in various industries, including office workstations, manufacturing facilities, healthcare settings, and construction sites. They learn how to recognize ergonomic hazards such as poor workstation setup, improper lifting techniques, repetitive motions, and awkward postures.
4. Prevention Strategies: Participants learn about effective strategies for preventing ergonomic-related injuries in the workplace. This includes implementing ergonomic design principles in workstations and tools, providing ergonomic training to employees, promoting proper lifting techniques, and encouraging regular breaks and stretches.
5. Workstation Design and Layout: Participants learn how to design and arrange workstations to minimize ergonomic risks and promote comfort and productivity. They learn about ergonomic furniture, adjustable chairs, ergonomic keyboards and mice, monitor placement, and other factors that contribute to a healthy and ergonomic workspace.
6. Employee Education and Training: The training emphasizes the importance of educating employees about ergonomics and providing them with training on proper ergonomic practices. Participants learn how to communicate the importance of ergonomics to employees, encourage them to report ergonomic issues, and empower them to take proactive measures to prevent injuries.
7. Continuous Improvement: Participants learn about the importance of continuous improvement in ergonomic risk management. They learn how to monitor and evaluate ergonomic interventions, solicit feedback from employees, and make adjustments as needed to ensure ongoing effectiveness.
Our Ergonomic Risk Areas and Prevention training program is conducted by certified ergonomics professionals with expertise in injury prevention and workplace safety. By completing this training, participants gain the knowledge and skills necessary to identify ergonomic hazards, implement preventive measures, and create a safer and more comfortable work environment for employees.
Occupational Health Assessment services in Kenya are designed to evaluate and manage the health risks associated with workplace activities and environments. Here’s an overview of our Occupational Health Assessment:
1. Hazard Identification: Our assessments begin with a comprehensive review of workplace activities, processes, and exposures to identify potential health hazards. This includes physical, chemical, biological, ergonomic, and psychosocial hazards that may impact employees’ health and well-being.
2. Risk Assessment: We assess the severity and likelihood of health risks identified during the hazard identification process. This involves evaluating exposure levels, duration of exposure, susceptibility of workers, and potential health effects. Our goal is to prioritize risks based on their significance and develop appropriate control measures.
3. Health Surveillance: We may recommend health surveillance programs to monitor the health status of employees exposed to specific occupational hazards. This may include periodic medical examinations, biological monitoring, and health assessments to detect early signs of occupational illnesses or injuries.
4. Ergonomic Assessment: Our assessments include an evaluation of ergonomic factors that may contribute to musculoskeletal disorders (MSDs) and other ergonomic-related injuries. We examine workstations, tools, equipment, and work practices to identify ergonomic risks and recommend ergonomic interventions to prevent injuries.
5. Chemical Exposure Assessment: We conduct exposure assessments to evaluate employees’ exposure to hazardous chemicals in the workplace. This includes air monitoring, personal sampling, and exposure modeling to determine potential health risks associated with chemical exposures. We provide recommendations to minimize exposure levels and ensure compliance with occupational exposure limits.
6. Psychosocial Risk Assessment: We assess psychosocial hazards such as workplace stress, bullying, harassment, and organizational culture factors that may impact employees’ mental health and well-being. We conduct surveys, interviews, and observations to identify psychosocial risks and develop strategies to promote a positive work environment.
7. Report and Recommendations: We provide detailed reports summarizing our findings, including identified hazards, risk assessments, and recommendations for hazard control measures. Our recommendations prioritize preventive measures to eliminate or minimize occupational health risks, protect employees’ health, and improve overall workplace safety and well-being.
Our Occupational Health Assessment services are conducted by experienced occupational health professionals who adhere to local regulations and international best practices. By investing in occupational health assessments, organizations can proactively manage health risks, comply with legal requirements, and promote a safe and healthy work environment for employees.
Our Manual Handling Training program in Kenya is designed to educate participants on safe manual handling practices to prevent musculoskeletal injuries and promote workplace safety. Here’s an overview of the training:
1. Understanding Manual Handling: Participants learn about the risks associated with manual handling tasks, including lifting, carrying, pushing, and pulling heavy objects. They gain an understanding of the anatomy and mechanics of the spine and muscles involved in manual handling activities.
2. Manual Handling Hazards: The training covers common hazards associated with manual handling, such as overexertion, awkward postures, repetitive motions, and environmental factors. Participants learn how these hazards can contribute to musculoskeletal disorders (MSDs) and other injuries.
3. Risk Assessment: Participants learn how to conduct manual handling risk assessments to identify hazards and assess the risks associated with specific tasks. They learn how to evaluate factors such as load weight, size, shape, stability, frequency, duration, and environmental conditions.
4. Safe Handling Techniques: The training teaches participants proper lifting and handling techniques to reduce the risk of injury. This includes techniques for lifting from the floor, waist height, and overhead, as well as team lifting and using mechanical aids. Participants also learn about maintaining neutral spine alignment, using the legs to lift, and avoiding twisting and bending motions.
5. Ergonomic Principles: Participants learn about ergonomic principles that can help reduce the risk of injury during manual handling tasks. This includes adjusting workstations and equipment to minimize reaching and stretching, improving grip and handling surfaces, and reducing the need for manual lifting through automation or mechanization.
6. Practical Exercises: The training includes hands-on practical exercises where participants practice safe manual handling techniques under the guidance of experienced instructors. This allows participants to apply their knowledge in a controlled environment and receive feedback on their technique.
7. Injury Prevention Strategies: Participants learn about strategies for preventing manual handling injuries in the workplace. This includes promoting a culture of safety, providing training and education to employees, implementing ergonomic improvements, and encouraging early reporting of injuries or discomfort.
Our Manual Handling Training program is delivered by certified instructors with expertise in manual handling safety and ergonomics. By completing this training, participants gain the knowledge and skills necessary to perform manual handling tasks safely, reduce the risk of injury, and promote a healthier and safer work environment.
Our Mental Health Training program in Kenya is designed to raise awareness, reduce stigma, and promote mental well-being in the workplace. Here’s an overview of the training:
1. Understanding Mental Health: Participants learn about common mental health conditions such as depression, anxiety, stress, and burnout. They gain an understanding of the signs and symptoms of mental health problems and how they can impact an individual’s well-being and performance.
2. Stigma Reduction: The training addresses stigma surrounding mental health and encourages open dialogue and acceptance. Participants learn about the importance of creating a supportive and non-judgmental environment where individuals feel comfortable seeking help and support.
3. Mental Health Awareness: Participants learn how to recognize signs of mental distress in themselves and others. They learn about the impact of stress, work-related pressures, and life events on mental health, as well as coping strategies for managing stress and promoting resilience.
4. Communication Skills: The training includes communication skills development to facilitate supportive conversations about mental health. Participants learn how to listen actively, show empathy, validate feelings, and offer appropriate support to colleagues who may be struggling with mental health issues.
5. Self-Care and Well-being: Participants learn about the importance of self-care and well-being practices for maintaining good mental health. They learn about strategies for managing stress, practicing mindfulness, maintaining work-life balance, and accessing support resources.
6. Creating a Mentally Healthy Workplace: Participants learn about strategies for creating a mentally healthy workplace culture. This includes promoting work-life balance, reducing stigma, fostering social connections, providing mental health resources and support services, and implementing policies and practices that prioritize employee well-being.
7. Crisis Response and Support: Participants learn about crisis response protocols and how to provide support to colleagues in crisis. They learn how to recognize signs of a mental health crisis, initiate appropriate interventions, and connect individuals with professional support services when needed.
Our Mental Health Training program is delivered by certified mental health professionals with expertise in workplace mental health. By completing this training, participants gain the knowledge and skills necessary to support mental well-being in the workplace, reduce stigma, and create a supportive environment where employees can thrive.
Our Chemical Safe Use training program in Kenya is designed to educate participants on the safe handling, storage, and use of hazardous chemicals in the workplace. Here’s an overview of the training:
1. Hazard Identification: Participants learn how to identify hazardous chemicals commonly used in the workplace and recognize their associated risks. They gain an understanding of chemical labels, safety data sheets (SDS), and hazard symbols to effectively identify chemical hazards.
2. Risk Assessment: The training covers the process of conducting risk assessments for chemical hazards to determine potential risks to health and safety. Participants learn how to assess exposure routes, toxicity levels, and control measures to mitigate risks associated with chemical use.
3. Safe Handling Practices: Participants learn best practices for safely handling chemicals, including proper storage, transportation, and disposal procedures. They learn how to use personal protective equipment (PPE), such as gloves, goggles, and respiratory protection, to minimize exposure to hazardous chemicals.
4. Emergency Response: The training includes instruction on responding to chemical spills, leaks, and other emergencies. Participants learn how to safely contain spills, evacuate affected areas, and implement emergency response protocols to minimize exposure and prevent injuries.
5. Chemical Compatibility: Participants learn about chemical compatibility and the potential hazards associated with mixing incompatible chemicals. They gain an understanding of the importance of segregating incompatible chemicals and following proper storage and handling procedures to prevent reactions.
6. Health Effects: Participants learn about the potential health effects associated with exposure to hazardous chemicals, including acute and chronic effects. They gain an understanding of routes of exposure, such as inhalation, ingestion, and skin contact, and how to prevent exposure through proper handling and use.
7. Regulatory Compliance: The training covers relevant regulations and standards governing the safe use of chemicals in the workplace, including OSHA’s Hazard Communication Standard (HCS) and chemical labeling requirements. Participants learn about their responsibilities as employers and employees to ensure compliance with these regulations.
Our Chemical Safe Use training program is delivered by certified instructors with expertise in chemical safety and occupational health. By completing this training, participants gain the knowledge and skills necessary to safely handle hazardous chemicals, minimize risks, and protect themselves and others from potential harm in the workplace.
Our Safety Leadership Training program in Kenya is designed to empower leaders at all levels of an organization to promote and foster a culture of safety, accountability, and continuous improvement. Here’s an overview of the training:
1. Understanding Safety Leadership: Participants learn about the critical role of leadership in creating and maintaining a safe work environment. They gain an understanding of safety leadership principles, behaviors, and attitudes that influence safety culture and performance.
2. Setting the Tone: The training emphasizes the importance of leaders setting a positive example and demonstrating a commitment to safety in their words and actions. Participants learn how to communicate safety expectations, priorities, and goals effectively to employees at all levels of the organization.
3. Leading by Example: Participants learn how to lead by example by consistently following safety protocols, wearing personal protective equipment (PPE), and adhering to safety procedures. They learn how their behaviors and decisions impact employee perceptions and attitudes towards safety.
4. Empowering Employees: The training teaches leaders how to empower employees to take ownership of safety and participate actively in safety initiatives. Participants learn how to involve employees in safety decision-making, problem-solving, and hazard reporting to create a culture of shared responsibility.
5. Safety Communication: Participants learn effective communication strategies for promoting safety awareness, sharing safety information, and addressing safety concerns. They learn how to conduct safety meetings, toolbox talks, and safety observations to engage employees and reinforce safety messages.
6. Coaching and Feedback: The training includes instruction on providing constructive feedback and coaching to employees to improve safety performance. Participants learn how to recognize and reinforce safe behaviors, address unsafe behaviors promptly, and provide support and guidance to employees to help them work safely.
7. Continuous Improvement: The training emphasizes the importance of continuous improvement in safety performance and practices. Participants learn how to conduct safety assessments, identify opportunities for improvement, implement corrective actions, and track progress towards safety goals.
8. Leading Change: Participants learn how to lead and manage change effectively to improve safety outcomes. They learn how to overcome resistance to change, communicate the benefits of safety initiatives, and engage employees in the change process to drive positive results.
Our Safety Leadership Training program is delivered by experienced instructors with expertise in safety leadership and organizational development. By completing this training, participants gain the knowledge and skills necessary to lead safety initiatives, inspire others to prioritize safety, and create a culture of safety excellence within their organizations.
Our Behavior-Based Safety (BBS) Training program in Kenya focuses on empowering employees to actively participate in creating a safer work environment by identifying and addressing at-risk behaviors. Here’s an overview of the training:
1. Understanding Behavior-Based Safety: Participants learn about the principles and concepts of behavior-based safety, which emphasize the influence of human behavior on safety outcomes. They gain an understanding of how behavior-based safety differs from traditional safety approaches and its role in preventing accidents and injuries.
2. Observation Skills: The training teaches participants how to effectively observe and identify both safe and at-risk behaviors in the workplace. Participants learn how to conduct behavior observations using observation checklists and other tools to collect data on behavior patterns and trends.
3. Positive Reinforcement: Participants learn about the importance of positive reinforcement in promoting safe behaviors. They learn how to provide constructive feedback and recognition to employees who demonstrate safe behaviors, reinforcing a culture of safety and accountability.
4. Hazard Recognition: Participants learn how to recognize and assess hazards associated with at-risk behaviors. They gain an understanding of how at-risk behaviors contribute to accidents and injuries and how to intervene to prevent potential incidents.
5. Communication Skills: The training includes instruction on effective communication skills for providing feedback and coaching to employees. Participants learn how to communicate observations and safety concerns in a respectful and non-confrontational manner, encouraging open dialogue and collaboration.
6. Empowerment and Engagement: Participants learn how to empower employees to take ownership of safety and participate actively in behavior-based safety initiatives. They learn how to involve employees in setting safety goals, identifying improvement opportunities, and developing solutions to address safety concerns.
7. Continuous Improvement: The training emphasizes the importance of continuous improvement in behavior-based safety practices. Participants learn how to analyze behavior observation data, identify trends and patterns, and implement proactive measures to address underlying causes of at-risk behaviors.
8. Leadership Support: The training includes a focus on the role of leadership in supporting behavior-based safety initiatives. Participants learn how to engage leaders and managers in promoting and championing behavior-based safety efforts, fostering a culture of safety at all levels of the organization.
Our Behavior-Based Safety Training program is delivered by experienced instructors with expertise in behavior-based safety methodologies. By completing this training, participants gain the knowledge and skills necessary to effectively observe behaviors, intervene to prevent incidents, and drive continuous improvement in safety performance.
Our Emergency Communication and Response Training program in Kenya is designed to prepare employees to effectively respond to emergencies and communicate critical information to ensure the safety and well-being of all individuals in the workplace. Here’s an overview of the training:
1. Emergency Preparedness: Participants learn about the importance of emergency preparedness and the potential risks and hazards that may occur in the workplace. They gain an understanding of the types of emergencies that could occur, such as fires, natural disasters, medical emergencies, and hazardous material spills.
2. Emergency Communication Protocols: The training covers established communication protocols and procedures for reporting emergencies and communicating critical information to appropriate personnel and authorities. Participants learn how to use communication devices such as telephones, two-way radios, and emergency notification systems effectively.
3. Incident Command System (ICS): Participants learn about the Incident Command System (ICS) and its role in coordinating emergency response efforts. They gain an understanding of ICS structure, roles, and responsibilities, including incident commanders, safety officers, and communication officers.
4. Effective Communication Strategies: Participants learn effective communication strategies for conveying clear and concise information during emergencies. They learn how to remain calm under pressure, assess the situation quickly, and communicate instructions and updates to employees, emergency responders, and other stakeholders.
5. Role-Specific Training: The training includes role-specific training for employees assigned specific emergency response roles, such as fire wardens, first aiders, and evacuation coordinators. Participants learn their responsibilities and duties during emergencies and how to effectively carry out their roles to ensure a coordinated response.
6. Evacuation Procedures: Participants learn about evacuation procedures, including evacuation routes, assembly points, and procedures for assisting individuals with disabilities or special needs. They learn how to conduct orderly evacuations, account for all individuals, and provide assistance to those in need during evacuations.
7. Mock Drills and Simulations: The training includes hands-on mock drills and simulations to practice emergency response procedures in a controlled environment. Participants have the opportunity to apply their knowledge and skills in realistic scenarios and receive feedback on their performance.
8. Post-Emergency Debriefing: Participants learn about the importance of post-emergency debriefing and analysis to identify lessons learned, areas for improvement, and best practices. They learn how to conduct debriefing sessions to review the effectiveness of emergency response efforts and make recommendations for future enhancements.
Our Emergency Communication and Response Training program is delivered by experienced instructors with expertise in emergency management and response. By completing this training, participants gain the knowledge and skills necessary to effectively respond to emergencies, communicate critical information, and ensure the safety of all individuals in the workplace.
Our Permit to Work Training program in Kenya educates participants on the procedures and protocols for obtaining and using permits to work safely in potentially hazardous environments or when performing high-risk tasks. Here’s an overview of the training:
1. Understanding Permit to Work Systems: Participants learn about the purpose and importance of permit to work systems in controlling hazardous work activities. They gain an understanding of the types of work activities that require permits, such as hot work, confined space entry, electrical work, and working at height.
2. Permitting Process: The training covers the step-by-step process for obtaining and using permits to work. Participants learn about the roles and responsibilities of key personnel involved in the permitting process, including permit issuers, authorized workers, and permit receivers.
3. Permit Types and Requirements: Participants learn about different types of permits to work and their specific requirements. This includes permits for hot work, confined space entry, excavation work, electrical work, and work at height. Participants learn how to determine which permits are required for specific tasks and how to complete permit application forms.
4. Risk Assessment and Control Measures: The training emphasizes the importance of conducting risk assessments before issuing permits to work. Participants learn how to assess the hazards associated with specific work activities, evaluate the risks, and implement appropriate control measures to mitigate risks and ensure safety.
5. Permit Conditions and Limitations: Participants learn about the conditions and limitations specified in permits to work, including time limitations, location restrictions, equipment requirements, and communication protocols. They learn how to communicate permit conditions to authorized workers and ensure compliance with permit requirements.
6. Monitoring and Compliance: The training covers procedures for monitoring work activities covered by permits to ensure compliance with permit conditions and safety requirements. Participants learn how to conduct periodic inspections, audits, and checks to verify that work is being performed safely and in accordance with permit specifications.
7. Emergency Response Procedures: Participants learn about emergency response procedures related to permit to work activities. They gain an understanding of how to respond to emergencies, evacuate workers from hazardous areas, and initiate emergency shutdown procedures if necessary.
8. Documentation and Record Keeping: The training includes instruction on the importance of maintaining accurate documentation and records related to permits to work. Participants learn how to complete permit documentation, record work activities, and retain records for auditing and regulatory compliance purposes.
Our Permit to Work Training program is delivered by experienced instructors with expertise in permit to work systems and safety management. By completing this training, participants gain the knowledge and skills necessary to effectively manage permit to work processes, control hazardous work activities, and ensure the safety of workers in the workplace.
Our workplace safety training programs in Kenya cover essential topics such as First Aid, Fire Safety, and Occupational Safety and Health (OSH), ensuring that organizations and individuals are equipped with the knowledge and skills to create a safe and healthy work environment. Here's an overview of each training:
1. First Aid Training: Our First Aid training equips participants with life-saving skills and knowledge to provide immediate assistance in medical emergencies. Topics include CPR (Cardiopulmonary Resuscitation), wound care, fracture management, choking relief, and emergency response protocols. Participants learn how to assess situations, administer first aid treatments, and effectively communicate with emergency services.
2. Fire Safety Training: Our Fire Safety training educates participants on fire prevention, evacuation procedures, and proper use of fire extinguishers and other firefighting equipment. Topics include fire detection, fire hazards identification, emergency evacuation plans, fire suppression techniques, and post-fire procedures. Participants learn how to respond effectively to fire emergencies, minimize risks, and protect lives and property.
3. Occupational Safety and Health (OSH) Training: Our OSH training focuses on promoting safe work practices and preventing workplace injuries and illnesses. Topics include hazard identification, risk assessment, personal protective equipment (PPE) usage, ergonomics, chemical safety, electrical safety, and machine guarding. Participants learn how to recognize and mitigate workplace hazards, comply with OSH regulations, and foster a culture of safety in the workplace.
Our training programs are interactive, engaging, and conducted by experienced instructors with expertise in their respective fields. We offer flexible training formats, including classroom sessions, hands-on demonstrations, simulations, and online modules, to accommodate the needs and preferences of participants. By investing in workplace safety training, organizations demonstrate their commitment to protecting their employees, reducing accidents and injuries, and promoting a culture of safety and well-being.
Our Work at Height, Scaffolding, and Rope Access training programs in Kenya are designed to equip participants with the knowledge and skills necessary to perform tasks safely and effectively in elevated environments. Here's an overview of each training:
1. Work at Height Training: Our Work at Height training focuses on identifying hazards associated with working at elevated levels and implementing controls to mitigate risks. Participants learn about fall protection systems, including personal fall arrest systems (PFAS), guardrails, and safety nets. Topics include risk assessment, ladder safety, scaffolding, working on roofs, and emergency response procedures. The training emphasizes the importance of planning, proper equipment usage, and adherence to safety regulations to prevent falls and accidents.
2. Scaffolding Training: Our Scaffolding training provides participants with comprehensive knowledge of scaffolding systems, components, assembly, and inspection procedures. Participants learn how to erect, dismantle, and inspect scaffolds safely, ensuring stability and structural integrity. Topics include scaffold types (e.g., supported scaffolds, suspended scaffolds), scaffold hazards, load capacities, fall protection measures, and regulatory requirements. The training covers best practices for scaffold erection, maintenance, and usage to prevent accidents and ensure a secure working platform.
3. Rope Access Training: Our Rope Access training equips participants with the skills needed to perform work tasks in challenging environments using rope access techniques. Participants learn rope rigging, anchor systems, descent, ascent, and rescue procedures. Topics include rope access equipment usage, safety protocols, communication techniques, and emergency response planning. The training emphasizes risk management, teamwork, and adherence to industry standards (e.g., IRATA, SPRAT) to ensure safe and efficient operations at height.
Our training programs combine theoretical knowledge with practical exercises and hands-on demonstrations to enhance participant learning and retention. Certified instructors with extensive experience in work at height, scaffolding, and rope access deliver the training, ensuring high-quality instruction and compliance with industry standards. By investing in these training programs, organizations demonstrate their commitment to worker safety, compliance with regulations, and prevention of accidents and injuries in elevated work environments.
Our Scissor Lift Training program in Kenya provides comprehensive instruction on the safe operation and maintenance of scissor lifts, ensuring that participants have the knowledge and skills necessary to work confidently and effectively with this equipment. Here's an overview of the training:
1. Equipment Familiarization: Participants learn about the various components and controls of scissor lifts, including platform controls, emergency stop mechanisms, hydraulic systems, and safety features. They gain an understanding of the different types of scissor lifts and their specific applications.
2. Safe Operation Practices: The training covers safe operating procedures for scissor lifts, including pre-operation inspections, proper positioning and leveling, safe ascent and descent, maneuvering in confined spaces, and working at height. Participants learn how to identify and avoid hazards such as overhead obstructions, uneven terrain, electrical hazards, and fall risks.
3. Fall Protection and Personal Safety: Participants learn about the importance of fall protection measures when working on scissor lifts, including the use of guardrails, personal fall arrest systems (PFAS), and restraint systems. They also receive instruction on wearing appropriate personal protective equipment (PPE) such as harnesses, hard hats, and safety footwear.
4. Emergency Procedures: The training covers emergency response procedures, including how to safely evacuate a scissor lift in the event of power failure or mechanical malfunction. Participants learn how to use emergency descent devices and rescue equipment, as well as how to communicate effectively during emergencies.
5. Maintenance and Inspections: Participants receive guidance on conducting routine maintenance tasks and pre-operation inspections to ensure that scissor lifts are in safe working condition. They learn how to identify and report equipment defects or deficiencies that could affect safety.
Our Scissor Lift Training program combines classroom instruction with hands-on practical exercises to reinforce learning and skill development. Certified instructors with expertise in scissor lift operations deliver the training, ensuring compliance with industry standards and regulations. By completing this training, participants gain the confidence and competence to operate scissor lifts safely, reducing the risk of accidents and injuries in the workplace.
Our Ladder Inspection Training program in Kenya provides comprehensive instruction on the proper inspection and maintenance of ladders to ensure they are safe for use in the workplace. Here's an overview of the training:
1. Ladder Types and Components: Participants learn about different types of ladders commonly used in various industries, including step ladders, extension ladders, and platform ladders. They gain an understanding of ladder components, such as rungs, rails, feet, and safety features.
2. Inspection Procedures: The training covers detailed inspection procedures for ladders, including pre-use inspections, periodic inspections, and post-incident inspections. Participants learn how to visually inspect ladders for signs of damage, wear, corrosion, or defects that could compromise safety.
3. Common Defects and Hazards: Participants are trained to recognize common defects and hazards associated with ladders, such as bent or broken rungs, loose or missing hardware, damaged rails, and worn-out feet. They learn how to assess the severity of defects and determine whether a ladder is safe for use or requires repair or replacement.
4. Maintenance and Repair: Participants receive guidance on proper maintenance practices to keep ladders in good working condition, including cleaning, lubrication, and storage. They learn how to perform minor repairs and adjustments to address minor defects and ensure ladder safety.
5. Regulatory Compliance: The training covers relevant regulations and standards governing ladder safety, including OSHA regulations, ANSI standards, and industry best practices. Participants learn about their responsibilities as employers and employees to ensure compliance with safety regulations and prevent accidents and injuries.
6. Hands-On Exercises: The training includes hands-on exercises where participants practice inspecting ladders and identifying defects under the guidance of experienced instructors. This practical component reinforces learning and helps participants develop confidence in their inspection skills.
Our Ladder Inspection Training program is conducted by certified instructors with expertise in ladder safety and inspection. By completing this training, participants gain the knowledge and skills necessary to conduct thorough ladder inspections, identify potential hazards, and take appropriate corrective actions to prevent accidents and ensure a safe work environment.
Our Work Equipment Risk Assessment training program in Kenya provides participants with the knowledge and skills needed to conduct comprehensive risk assessments for various types of work equipment. Here's an overview of the training:
1. Understanding Work Equipment: Participants learn about different types of work equipment commonly used in the workplace, including machinery, tools, vehicles, and lifting equipment. They gain an understanding of the hazards associated with each type of equipment and the potential risks to workers' health and safety.
2. Risk Assessment Principles: The training covers the principles of risk assessment, including hazard identification, risk analysis, risk evaluation, and risk control measures. Participants learn how to systematically identify hazards associated with work equipment, assess the likelihood and severity of potential consequences, and prioritize risks for mitigation.
3. Risk Assessment Process: Participants are guided through the step-by-step process of conducting a work equipment risk assessment. They learn how to gather relevant information, assess hazards and risks, determine appropriate control measures, and document findings. Practical examples and case studies are used to illustrate key concepts and techniques.
4. Hazard Control Measures: Participants learn about various control measures that can be implemented to mitigate risks associated with work equipment. This includes engineering controls, administrative controls, and personal protective equipment (PPE). Emphasis is placed on the hierarchy of controls, with a focus on eliminating or minimizing hazards at the source.
5. Legal Requirements and Standards: The training covers relevant legal requirements and industry standards related to work equipment safety and risk assessment. Participants learn about their obligations under local regulations, such as the Occupational Safety and Health Act, as well as international standards, such as ISO 12100 and ISO 45001.
6. Practical Exercises: The training includes practical exercises where participants apply their knowledge and skills to conduct risk assessments for specific work equipment scenarios. This hands-on experience allows participants to practice identifying hazards, assessing risks, and developing control measures in a controlled environment.
Our Work Equipment Risk Assessment training program is delivered by experienced instructors with expertise in risk management and occupational safety. By completing this training, participants gain the confidence and competence to effectively assess risks associated with work equipment, implement appropriate control measures, and contribute to a safer work environment.
Our Hot Works Risk Assessment Training in Kenya equips participants with the knowledge and skills necessary to conduct thorough risk assessments for hot work activities, ensuring the safety of workers and the surrounding environment. Here's an overview of the training:
1. Understanding Hot Work: Participants gain an understanding of what constitutes hot work, including activities such as welding, cutting, brazing, soldering, and grinding. They learn about the hazards associated with hot work, including fire, explosion, burns, and toxic fumes.
2. Regulatory Requirements: The training covers relevant regulations and standards governing hot work safety, including local occupational health and safety regulations, fire codes, and industry best practices. Participants learn about their legal obligations and responsibilities when performing hot work activities.
3. Risk Assessment Principles: Participants learn the principles of risk assessment as they apply to hot work activities. They learn how to systematically identify hazards, assess the likelihood and severity of potential consequences, and prioritize risks for mitigation. Emphasis is placed on the importance of proactive risk management to prevent accidents and injuries.
4. Hazard Identification: Participants learn how to identify common hazards associated with hot work activities, including flammable materials, combustible dusts, confined spaces, and nearby equipment or structures. They learn how to assess the risks posed by these hazards and determine appropriate control measures.
5. Control Measures: Participants learn about various control measures that can be implemented to mitigate risks associated with hot work activities. This includes implementing safe work procedures, providing appropriate personal protective equipment (PPE), using fire-resistant barriers and shields, and implementing fire prevention measures.
6. Hot Work Permit Systems: Participants learn about the importance of implementing a hot work permit system to control and monitor hot work activities. They learn about the key components of a hot work permit system, including permit issuance, pre-work inspections, fire watch requirements, and post-work checks.
7. Practical Exercises: The training includes practical exercises where participants apply their knowledge and skills to conduct hot work risk assessments for specific scenarios. This hands-on experience allows participants to practice hazard identification, risk assessment, and control measure selection in a controlled environment.
Our Hot Works Risk Assessment Training is conducted by experienced instructors with expertise in hot work safety and risk management. By completing this training, participants gain the confidence and competence to effectively assess risks associated with hot work activities, implement appropriate control measures, and ensure the safety of workers and the workplace.
Our Ergonomic Risk Areas and Prevention training program in Kenya focuses on identifying ergonomic hazards in the workplace and implementing strategies to prevent musculoskeletal disorders (MSDs) and other ergonomic-related injuries. Here's an overview of the training:
1. Understanding Ergonomics: Participants learn about the principles of ergonomics and how they apply to the workplace. They gain an understanding of how ergonomic factors such as posture, repetitive motions, force exertion, and awkward positions can contribute to MSDs and other injuries.
2. Ergonomic Risk Assessment: The training covers the process of conducting ergonomic risk assessments to identify potential hazards in the workplace. Participants learn how to observe work tasks, identify ergonomic risk factors, assess their severity and frequency, and prioritize areas for intervention.
3. Common Ergonomic Risk Areas: Participants learn about common ergonomic risk areas in various industries, including office workstations, manufacturing facilities, healthcare settings, and construction sites. They learn how to recognize ergonomic hazards such as poor workstation setup, improper lifting techniques, repetitive motions, and awkward postures.
4. Prevention Strategies: Participants learn about effective strategies for preventing ergonomic-related injuries in the workplace. This includes implementing ergonomic design principles in workstations and tools, providing ergonomic training to employees, promoting proper lifting techniques, and encouraging regular breaks and stretches.
5. Workstation Design and Layout: Participants learn how to design and arrange workstations to minimize ergonomic risks and promote comfort and productivity. They learn about ergonomic furniture, adjustable chairs, ergonomic keyboards and mice, monitor placement, and other factors that contribute to a healthy and ergonomic workspace.
6. Employee Education and Training: The training emphasizes the importance of educating employees about ergonomics and providing them with training on proper ergonomic practices. Participants learn how to communicate the importance of ergonomics to employees, encourage them to report ergonomic issues, and empower them to take proactive measures to prevent injuries.
7. Continuous Improvement: Participants learn about the importance of continuous improvement in ergonomic risk management. They learn how to monitor and evaluate ergonomic interventions, solicit feedback from employees, and make adjustments as needed to ensure ongoing effectiveness.
Our Ergonomic Risk Areas and Prevention training program is conducted by certified ergonomics professionals with expertise in injury prevention and workplace safety. By completing this training, participants gain the knowledge and skills necessary to identify ergonomic hazards, implement preventive measures, and create a safer and more comfortable work environment for employees.
Occupational Health Assessment services in Kenya are designed to evaluate and manage the health risks associated with workplace activities and environments. Here's an overview of our Occupational Health Assessment:
1. Hazard Identification: Our assessments begin with a comprehensive review of workplace activities, processes, and exposures to identify potential health hazards. This includes physical, chemical, biological, ergonomic, and psychosocial hazards that may impact employees' health and well-being.
2. Risk Assessment: We assess the severity and likelihood of health risks identified during the hazard identification process. This involves evaluating exposure levels, duration of exposure, susceptibility of workers, and potential health effects. Our goal is to prioritize risks based on their significance and develop appropriate control measures.
3. Health Surveillance: We may recommend health surveillance programs to monitor the health status of employees exposed to specific occupational hazards. This may include periodic medical examinations, biological monitoring, and health assessments to detect early signs of occupational illnesses or injuries.
4. Ergonomic Assessment: Our assessments include an evaluation of ergonomic factors that may contribute to musculoskeletal disorders (MSDs) and other ergonomic-related injuries. We examine workstations, tools, equipment, and work practices to identify ergonomic risks and recommend ergonomic interventions to prevent injuries.
5. Chemical Exposure Assessment: We conduct exposure assessments to evaluate employees' exposure to hazardous chemicals in the workplace. This includes air monitoring, personal sampling, and exposure modeling to determine potential health risks associated with chemical exposures. We provide recommendations to minimize exposure levels and ensure compliance with occupational exposure limits.
6. Psychosocial Risk Assessment: We assess psychosocial hazards such as workplace stress, bullying, harassment, and organizational culture factors that may impact employees' mental health and well-being. We conduct surveys, interviews, and observations to identify psychosocial risks and develop strategies to promote a positive work environment.
7. Report and Recommendations: We provide detailed reports summarizing our findings, including identified hazards, risk assessments, and recommendations for hazard control measures. Our recommendations prioritize preventive measures to eliminate or minimize occupational health risks, protect employees' health, and improve overall workplace safety and well-being.
Our Occupational Health Assessment services are conducted by experienced occupational health professionals who adhere to local regulations and international best practices. By investing in occupational health assessments, organizations can proactively manage health risks, comply with legal requirements, and promote a safe and healthy work environment for employees.
Our Manual Handling Training program in Kenya is designed to educate participants on safe manual handling practices to prevent musculoskeletal injuries and promote workplace safety. Here's an overview of the training:
1. Understanding Manual Handling: Participants learn about the risks associated with manual handling tasks, including lifting, carrying, pushing, and pulling heavy objects. They gain an understanding of the anatomy and mechanics of the spine and muscles involved in manual handling activities.
2. Manual Handling Hazards: The training covers common hazards associated with manual handling, such as overexertion, awkward postures, repetitive motions, and environmental factors. Participants learn how these hazards can contribute to musculoskeletal disorders (MSDs) and other injuries.
3. Risk Assessment: Participants learn how to conduct manual handling risk assessments to identify hazards and assess the risks associated with specific tasks. They learn how to evaluate factors such as load weight, size, shape, stability, frequency, duration, and environmental conditions.
4. Safe Handling Techniques: The training teaches participants proper lifting and handling techniques to reduce the risk of injury. This includes techniques for lifting from the floor, waist height, and overhead, as well as team lifting and using mechanical aids. Participants also learn about maintaining neutral spine alignment, using the legs to lift, and avoiding twisting and bending motions.
5. Ergonomic Principles: Participants learn about ergonomic principles that can help reduce the risk of injury during manual handling tasks. This includes adjusting workstations and equipment to minimize reaching and stretching, improving grip and handling surfaces, and reducing the need for manual lifting through automation or mechanization.
6. Practical Exercises: The training includes hands-on practical exercises where participants practice safe manual handling techniques under the guidance of experienced instructors. This allows participants to apply their knowledge in a controlled environment and receive feedback on their technique.
7. Injury Prevention Strategies: Participants learn about strategies for preventing manual handling injuries in the workplace. This includes promoting a culture of safety, providing training and education to employees, implementing ergonomic improvements, and encouraging early reporting of injuries or discomfort.
Our Manual Handling Training program is delivered by certified instructors with expertise in manual handling safety and ergonomics. By completing this training, participants gain the knowledge and skills necessary to perform manual handling tasks safely, reduce the risk of injury, and promote a healthier and safer work environment.
Our Mental Health Training program in Kenya is designed to raise awareness, reduce stigma, and promote mental well-being in the workplace. Here's an overview of the training:
1. Understanding Mental Health: Participants learn about common mental health conditions such as depression, anxiety, stress, and burnout. They gain an understanding of the signs and symptoms of mental health problems and how they can impact an individual's well-being and performance.
2. Stigma Reduction: The training addresses stigma surrounding mental health and encourages open dialogue and acceptance. Participants learn about the importance of creating a supportive and non-judgmental environment where individuals feel comfortable seeking help and support.
3. Mental Health Awareness: Participants learn how to recognize signs of mental distress in themselves and others. They learn about the impact of stress, work-related pressures, and life events on mental health, as well as coping strategies for managing stress and promoting resilience.
4. Communication Skills: The training includes communication skills development to facilitate supportive conversations about mental health. Participants learn how to listen actively, show empathy, validate feelings, and offer appropriate support to colleagues who may be struggling with mental health issues.
5. Self-Care and Well-being: Participants learn about the importance of self-care and well-being practices for maintaining good mental health. They learn about strategies for managing stress, practicing mindfulness, maintaining work-life balance, and accessing support resources.
6. Creating a Mentally Healthy Workplace: Participants learn about strategies for creating a mentally healthy workplace culture. This includes promoting work-life balance, reducing stigma, fostering social connections, providing mental health resources and support services, and implementing policies and practices that prioritize employee well-being.
7. Crisis Response and Support: Participants learn about crisis response protocols and how to provide support to colleagues in crisis. They learn how to recognize signs of a mental health crisis, initiate appropriate interventions, and connect individuals with professional support services when needed.
Our Mental Health Training program is delivered by certified mental health professionals with expertise in workplace mental health. By completing this training, participants gain the knowledge and skills necessary to support mental well-being in the workplace, reduce stigma, and create a supportive environment where employees can thrive.
Our Chemical Safe Use training program in Kenya is designed to educate participants on the safe handling, storage, and use of hazardous chemicals in the workplace. Here's an overview of the training:
1. Hazard Identification: Participants learn how to identify hazardous chemicals commonly used in the workplace and recognize their associated risks. They gain an understanding of chemical labels, safety data sheets (SDS), and hazard symbols to effectively identify chemical hazards.
2. Risk Assessment: The training covers the process of conducting risk assessments for chemical hazards to determine potential risks to health and safety. Participants learn how to assess exposure routes, toxicity levels, and control measures to mitigate risks associated with chemical use.
3. Safe Handling Practices: Participants learn best practices for safely handling chemicals, including proper storage, transportation, and disposal procedures. They learn how to use personal protective equipment (PPE), such as gloves, goggles, and respiratory protection, to minimize exposure to hazardous chemicals.
4. Emergency Response: The training includes instruction on responding to chemical spills, leaks, and other emergencies. Participants learn how to safely contain spills, evacuate affected areas, and implement emergency response protocols to minimize exposure and prevent injuries.
5. Chemical Compatibility: Participants learn about chemical compatibility and the potential hazards associated with mixing incompatible chemicals. They gain an understanding of the importance of segregating incompatible chemicals and following proper storage and handling procedures to prevent reactions.
6. Health Effects: Participants learn about the potential health effects associated with exposure to hazardous chemicals, including acute and chronic effects. They gain an understanding of routes of exposure, such as inhalation, ingestion, and skin contact, and how to prevent exposure through proper handling and use.
7. Regulatory Compliance: The training covers relevant regulations and standards governing the safe use of chemicals in the workplace, including OSHA's Hazard Communication Standard (HCS) and chemical labeling requirements. Participants learn about their responsibilities as employers and employees to ensure compliance with these regulations.
Our Chemical Safe Use training program is delivered by certified instructors with expertise in chemical safety and occupational health. By completing this training, participants gain the knowledge and skills necessary to safely handle hazardous chemicals, minimize risks, and protect themselves and others from potential harm in the workplace.
Our Safety Leadership Training program in Kenya is designed to empower leaders at all levels of an organization to promote and foster a culture of safety, accountability, and continuous improvement. Here's an overview of the training:
1. Understanding Safety Leadership: Participants learn about the critical role of leadership in creating and maintaining a safe work environment. They gain an understanding of safety leadership principles, behaviors, and attitudes that influence safety culture and performance.
2. Setting the Tone: The training emphasizes the importance of leaders setting a positive example and demonstrating a commitment to safety in their words and actions. Participants learn how to communicate safety expectations, priorities, and goals effectively to employees at all levels of the organization.
3. Leading by Example: Participants learn how to lead by example by consistently following safety protocols, wearing personal protective equipment (PPE), and adhering to safety procedures. They learn how their behaviors and decisions impact employee perceptions and attitudes towards safety.
4. Empowering Employees: The training teaches leaders how to empower employees to take ownership of safety and participate actively in safety initiatives. Participants learn how to involve employees in safety decision-making, problem-solving, and hazard reporting to create a culture of shared responsibility.
5. Safety Communication: Participants learn effective communication strategies for promoting safety awareness, sharing safety information, and addressing safety concerns. They learn how to conduct safety meetings, toolbox talks, and safety observations to engage employees and reinforce safety messages.
6. Coaching and Feedback: The training includes instruction on providing constructive feedback and coaching to employees to improve safety performance. Participants learn how to recognize and reinforce safe behaviors, address unsafe behaviors promptly, and provide support and guidance to employees to help them work safely.
7. Continuous Improvement: The training emphasizes the importance of continuous improvement in safety performance and practices. Participants learn how to conduct safety assessments, identify opportunities for improvement, implement corrective actions, and track progress towards safety goals.
8. Leading Change: Participants learn how to lead and manage change effectively to improve safety outcomes. They learn how to overcome resistance to change, communicate the benefits of safety initiatives, and engage employees in the change process to drive positive results.
Our Safety Leadership Training program is delivered by experienced instructors with expertise in safety leadership and organizational development. By completing this training, participants gain the knowledge and skills necessary to lead safety initiatives, inspire others to prioritize safety, and create a culture of safety excellence within their organizations.
Our Behavior-Based Safety (BBS) Training program in Kenya focuses on empowering employees to actively participate in creating a safer work environment by identifying and addressing at-risk behaviors. Here's an overview of the training:
1. Understanding Behavior-Based Safety: Participants learn about the principles and concepts of behavior-based safety, which emphasize the influence of human behavior on safety outcomes. They gain an understanding of how behavior-based safety differs from traditional safety approaches and its role in preventing accidents and injuries.
2. Observation Skills: The training teaches participants how to effectively observe and identify both safe and at-risk behaviors in the workplace. Participants learn how to conduct behavior observations using observation checklists and other tools to collect data on behavior patterns and trends.
3. Positive Reinforcement: Participants learn about the importance of positive reinforcement in promoting safe behaviors. They learn how to provide constructive feedback and recognition to employees who demonstrate safe behaviors, reinforcing a culture of safety and accountability.
4. Hazard Recognition: Participants learn how to recognize and assess hazards associated with at-risk behaviors. They gain an understanding of how at-risk behaviors contribute to accidents and injuries and how to intervene to prevent potential incidents.
5. Communication Skills: The training includes instruction on effective communication skills for providing feedback and coaching to employees. Participants learn how to communicate observations and safety concerns in a respectful and non-confrontational manner, encouraging open dialogue and collaboration.
6. Empowerment and Engagement: Participants learn how to empower employees to take ownership of safety and participate actively in behavior-based safety initiatives. They learn how to involve employees in setting safety goals, identifying improvement opportunities, and developing solutions to address safety concerns.
7. Continuous Improvement: The training emphasizes the importance of continuous improvement in behavior-based safety practices. Participants learn how to analyze behavior observation data, identify trends and patterns, and implement proactive measures to address underlying causes of at-risk behaviors.
8. Leadership Support: The training includes a focus on the role of leadership in supporting behavior-based safety initiatives. Participants learn how to engage leaders and managers in promoting and championing behavior-based safety efforts, fostering a culture of safety at all levels of the organization.
Our Behavior-Based Safety Training program is delivered by experienced instructors with expertise in behavior-based safety methodologies. By completing this training, participants gain the knowledge and skills necessary to effectively observe behaviors, intervene to prevent incidents, and drive continuous improvement in safety performance.
Our Emergency Communication and Response Training program in Kenya is designed to prepare employees to effectively respond to emergencies and communicate critical information to ensure the safety and well-being of all individuals in the workplace. Here's an overview of the training:
1. Emergency Preparedness: Participants learn about the importance of emergency preparedness and the potential risks and hazards that may occur in the workplace. They gain an understanding of the types of emergencies that could occur, such as fires, natural disasters, medical emergencies, and hazardous material spills.
2. Emergency Communication Protocols: The training covers established communication protocols and procedures for reporting emergencies and communicating critical information to appropriate personnel and authorities. Participants learn how to use communication devices such as telephones, two-way radios, and emergency notification systems effectively.
3. Incident Command System (ICS): Participants learn about the Incident Command System (ICS) and its role in coordinating emergency response efforts. They gain an understanding of ICS structure, roles, and responsibilities, including incident commanders, safety officers, and communication officers.
4. Effective Communication Strategies: Participants learn effective communication strategies for conveying clear and concise information during emergencies. They learn how to remain calm under pressure, assess the situation quickly, and communicate instructions and updates to employees, emergency responders, and other stakeholders.
5. Role-Specific Training: The training includes role-specific training for employees assigned specific emergency response roles, such as fire wardens, first aiders, and evacuation coordinators. Participants learn their responsibilities and duties during emergencies and how to effectively carry out their roles to ensure a coordinated response.
6. Evacuation Procedures: Participants learn about evacuation procedures, including evacuation routes, assembly points, and procedures for assisting individuals with disabilities or special needs. They learn how to conduct orderly evacuations, account for all individuals, and provide assistance to those in need during evacuations.
7. Mock Drills and Simulations: The training includes hands-on mock drills and simulations to practice emergency response procedures in a controlled environment. Participants have the opportunity to apply their knowledge and skills in realistic scenarios and receive feedback on their performance.
8. Post-Emergency Debriefing: Participants learn about the importance of post-emergency debriefing and analysis to identify lessons learned, areas for improvement, and best practices. They learn how to conduct debriefing sessions to review the effectiveness of emergency response efforts and make recommendations for future enhancements.
Our Emergency Communication and Response Training program is delivered by experienced instructors with expertise in emergency management and response. By completing this training, participants gain the knowledge and skills necessary to effectively respond to emergencies, communicate critical information, and ensure the safety of all individuals in the workplace.
Our Permit to Work Training program in Kenya educates participants on the procedures and protocols for obtaining and using permits to work safely in potentially hazardous environments or when performing high-risk tasks. Here's an overview of the training:
1. Understanding Permit to Work Systems: Participants learn about the purpose and importance of permit to work systems in controlling hazardous work activities. They gain an understanding of the types of work activities that require permits, such as hot work, confined space entry, electrical work, and working at height.
2. Permitting Process: The training covers the step-by-step process for obtaining and using permits to work. Participants learn about the roles and responsibilities of key personnel involved in the permitting process, including permit issuers, authorized workers, and permit receivers.
3. Permit Types and Requirements: Participants learn about different types of permits to work and their specific requirements. This includes permits for hot work, confined space entry, excavation work, electrical work, and work at height. Participants learn how to determine which permits are required for specific tasks and how to complete permit application forms.
4. Risk Assessment and Control Measures: The training emphasizes the importance of conducting risk assessments before issuing permits to work. Participants learn how to assess the hazards associated with specific work activities, evaluate the risks, and implement appropriate control measures to mitigate risks and ensure safety.
5. Permit Conditions and Limitations: Participants learn about the conditions and limitations specified in permits to work, including time limitations, location restrictions, equipment requirements, and communication protocols. They learn how to communicate permit conditions to authorized workers and ensure compliance with permit requirements.
6. Monitoring and Compliance: The training covers procedures for monitoring work activities covered by permits to ensure compliance with permit conditions and safety requirements. Participants learn how to conduct periodic inspections, audits, and checks to verify that work is being performed safely and in accordance with permit specifications.
7. Emergency Response Procedures: Participants learn about emergency response procedures related to permit to work activities. They gain an understanding of how to respond to emergencies, evacuate workers from hazardous areas, and initiate emergency shutdown procedures if necessary.
8. Documentation and Record Keeping: The training includes instruction on the importance of maintaining accurate documentation and records related to permits to work. Participants learn how to complete permit documentation, record work activities, and retain records for auditing and regulatory compliance purposes.
Our Permit to Work Training program is delivered by experienced instructors with expertise in permit to work systems and safety management. By completing this training, participants gain the knowledge and skills necessary to effectively manage permit to work processes, control hazardous work activities, and ensure the safety of workers in the workplace.