Assessments and Audits
Our assessments and audits services in Kenya are comprehensive solutions designed to evaluate organizational processes, practices, and systems to ensure compliance, identify areas for improvement, and drive continuous performance enhancement. Through meticulous assessments and audits, we help organizations understand their current state, identify strengths, weaknesses, and areas of non-compliance, and develop actionable recommendations for improvement.
Our assessment services cover various aspects, including environmental, health, safety, and quality management systems. We conduct thorough evaluations, examining documentation, conducting interviews, and performing on-site inspections to assess organizational performance against regulatory requirements, industry standards, and best practices.
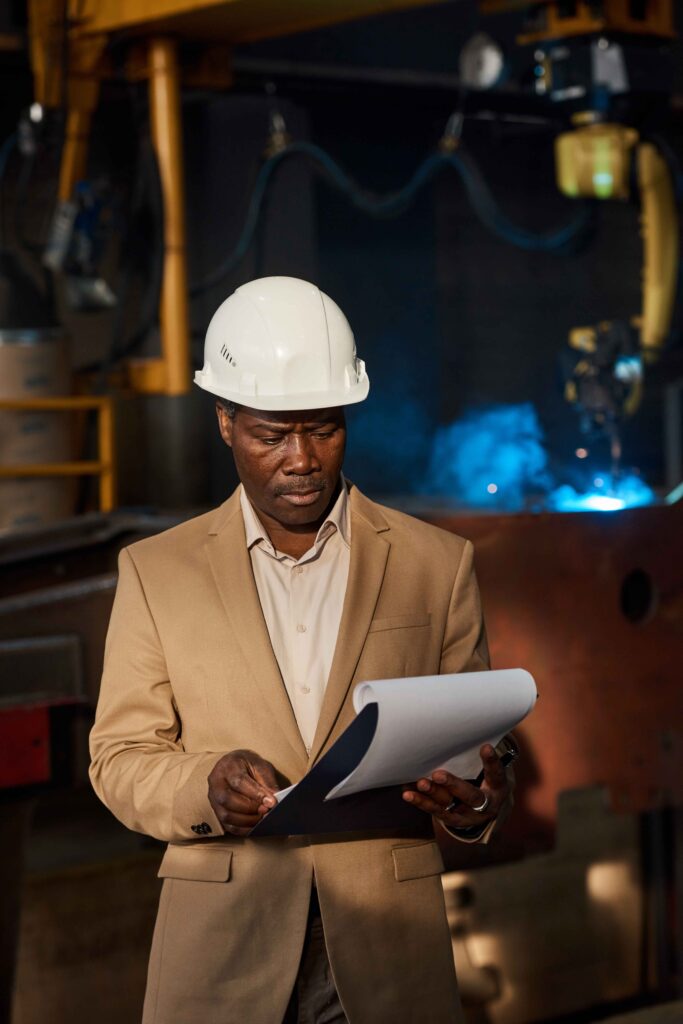
Similarly, our audit services involve systematic reviews of organizational processes and practices to verify compliance, identify gaps, and assess the effectiveness of management systems. Our experienced auditors utilize standardized methodologies and rigorous protocols to conduct audits objectively and impartially, providing clients with valuable insights and recommendations for improvement.
Whether it’s environmental compliance audits, health and safety inspections, or quality management system assessments, our goal is to help organizations in Kenya enhance their operational efficiency, minimize risks, and achieve their strategic objectives. By partnering with us for assessments and audits, organizations can demonstrate their commitment to excellence, drive continuous improvement, and maintain a competitive edge in today’s dynamic business environment.
Assesments & Audits
Our work equipment assessment and management services in Kenya provide organizations with comprehensive solutions to ensure the safety, reliability, and regulatory compliance of their work equipment. We conduct thorough assessments of all types of work equipment, including machinery, tools, vehicles, and personal protective equipment (PPE), to identify potential hazards, assess risks, and implement effective management strategies.
Our process begins with a detailed inspection and evaluation of work equipment to identify any defects, malfunctions, or safety concerns. We assess factors such as equipment design, condition, maintenance history, and operator training to determine compliance with relevant regulations and industry standards.
Based on our findings, we develop customized management plans tailored to the specific needs and requirements of each organization. These plans may include recommendations for equipment maintenance, repair, replacement, and training programs to ensure safe and efficient operation.
Throughout the management process, we provide ongoing support and guidance to help organizations implement and maintain effective work equipment management systems. Our goal is to help organizations minimize the risk of accidents, injuries, and equipment failures, while maximizing productivity and regulatory compliance.
By partnering with us for work equipment assessment and management, organizations in Kenya can enhance workplace safety, protect employees from harm, and demonstrate their commitment to excellence in equipment safety and management practices.
Our confined space risk assessment services in Kenya provide organizations with comprehensive evaluations to identify and mitigate hazards associated with confined spaces. We conduct thorough assessments of confined spaces, such as tanks, silos, sewers, and storage bins, to identify potential risks and ensure compliance with relevant regulations and industry standards.
Our process begins with a detailed inspection of confined spaces to identify potential hazards, such as limited entry and exit points, poor ventilation, hazardous atmospheres, and physical obstructions. We also assess factors such as the presence of hazardous materials, temperature extremes, and the need for specialized equipment or procedures.
Based on our findings, we develop customized risk assessment reports that outline the specific hazards present in each confined space, along with recommended control measures to mitigate risks and ensure the safety of workers. These measures may include implementing confined space entry permits, providing appropriate training and personal protective equipment (PPE), and implementing engineering controls to eliminate or minimize hazards.
Throughout the risk assessment process, we provide ongoing support and guidance to help organizations implement and maintain effective confined space safety programs. Our goal is to help organizations minimize the risk of accidents, injuries, and fatalities associated with confined space work, while ensuring compliance with regulatory requirements and industry best practices.
Our occupational safety and health audits in Kenya are comprehensive evaluations designed to assess and enhance workplace safety and health practices. We conduct thorough reviews of organizational policies, procedures, and practices to identify areas of non-compliance, potential hazards, and opportunities for improvement.
Our audits cover a wide range of occupational safety and health aspects, including hazard identification and risk assessment, emergency preparedness, training and competency, personal protective equipment (PPE) usage, ergonomics, and compliance with regulatory requirements such as the Occupational Safety and Health Act.
During the audit process, our experienced auditors utilize standardized methodologies and checklists to systematically assess the effectiveness of existing safety and health management systems. We conduct on-site inspections, interviews with employees, and review of documentation to gather relevant information and insights.
Based on our findings, we provide detailed audit reports outlining areas of strength and areas needing improvement, along with actionable recommendations for corrective actions and enhancements. These recommendations may include implementing new safety procedures, providing additional training, upgrading equipment, or improving workplace ergonomics.
Our goal is to help organizations create safer and healthier work environments, reduce the risk of accidents and injuries, and ensure compliance with occupational safety and health regulations. By partnering with us for occupational safety and health audits, organizations in Kenya can demonstrate their commitment to protecting their workforce and promoting a culture of safety excellence.
Our fire safety audits in Kenya provide organizations with thorough evaluations to assess and enhance their fire prevention and emergency preparedness measures. We conduct comprehensive reviews of facilities, systems, and procedures to identify fire hazards, assess risks, and ensure compliance with fire safety regulations and standards.
During the audit process, our experienced fire safety professionals conduct on-site inspections to evaluate factors such as building layout, fire detection and alarm systems, emergency exits, fire suppression equipment, electrical systems, storage of flammable materials, and evacuation procedures. We also review documentation, such as fire safety plans, maintenance records, and training records, to assess compliance with regulatory requirements.
Based on our findings, we provide detailed audit reports outlining areas of compliance, deficiencies, and recommendations for improvement. These recommendations may include implementing additional fire safety measures, conducting staff training and drills, upgrading fire protection systems, and improving emergency response procedures.
Our fire safety audits are designed to help organizations create safer work environments, reduce the risk of fire incidents, and protect lives and property. By partnering with us for fire safety audits, organizations in Kenya can demonstrate their commitment to fire safety excellence and ensure compliance with applicable regulations and standards.
Our display screen equipment (DSE) risk assessment services in Kenya focus on evaluating and mitigating potential ergonomic hazards associated with computer workstations and display screen equipment. We conduct thorough assessments to identify ergonomic risk factors, such as poor workstation setup, inadequate lighting, glare, and repetitive tasks, that can contribute to musculoskeletal disorders and other health issues.
During the assessment process, our experienced ergonomics specialists conduct on-site evaluations of workstations, including computer monitors, keyboards, mice, chairs, and desk setups. We assess factors such as monitor height and distance, keyboard and mouse placement, chair ergonomics, lighting conditions, and the overall workstation layout to identify areas of concern.
Through employee interviews and observation, we gather feedback on existing work practices, discomfort, and symptoms related to DSE use. We also review documentation, such as policies and procedures related to DSE use and ergonomics, to assess compliance with regulatory requirements and best practices.
Based on our findings, we provide detailed risk assessment reports outlining identified ergonomic hazards, associated risks, and recommendations for risk control and mitigation. These recommendations may include ergonomic workstation adjustments, changes to work practices, employee training on proper ergonomics, and provision of ergonomic equipment and accessories.
Our DSE risk assessment services help organizations create safer and more comfortable work environments for employees who use display screen equipment. By addressing ergonomic hazards proactively, organizations can reduce the risk of musculoskeletal disorders, improve employee comfort and productivity, and demonstrate their commitment to employee health and well-being.
Our occupational health assessments and audits in Kenya provide organizations with comprehensive evaluations to promote employee health and well-being in the workplace. We conduct thorough assessments of occupational health hazards and risks, including physical, chemical, biological, and psychosocial factors, to ensure compliance with occupational health regulations and standards.
During the assessment process, our experienced occupational health professionals conduct on-site inspections, employee surveys, and review of medical records to identify potential health hazards and assess the effectiveness of existing control measures. We evaluate factors such as exposure to hazardous substances, noise levels, ergonomic risks, work-related stress, and psychosocial factors to provide a holistic assessment of occupational health risks.
Through employee interviews and medical examinations, we gather information on existing health conditions, work-related symptoms, and occupational health concerns. We also assess organizational policies, procedures, and programs related to occupational health and employee wellness to identify areas for improvement.
Based on our findings, we provide detailed audit reports outlining identified occupational health hazards, associated risks, and recommendations for risk control and mitigation. These recommendations may include implementing engineering controls, administrative measures, providing personal protective equipment (PPE), or enhancing employee wellness programs and health promotion activities.
Our occupational health assessments and audits help organizations create healthier and safer work environments, reduce the risk of work-related illnesses and injuries, and improve overall employee well-being and productivity. By partnering with us for occupational health assessments and audits, organizations in Kenya can demonstrate their commitment to employee health and safety and ensure compliance with occupational health regulations and standards.
Our incident investigations and root cause analysis services in Kenya provide organizations with thorough evaluations to identify the underlying causes of workplace incidents and prevent their recurrence. We conduct comprehensive investigations into incidents such as accidents, near misses, injuries, and occupational illnesses to determine the root causes and contributing factors.
During the investigation process, our experienced safety professionals utilize proven methodologies and techniques to gather information, interview witnesses, and analyze evidence related to the incident. We examine factors such as equipment failures, human error, unsafe work practices, and deficiencies in safety management systems to identify root causes and underlying systemic issues.
Through root cause analysis, we delve deep into the sequence of events leading up to the incident to uncover the underlying causes, including organizational, procedural, and cultural factors. We prioritize corrective actions to address root causes and implement preventive measures to reduce the likelihood of similar incidents occurring in the future.
Our incident investigation and root cause analysis services are designed to help organizations learn from past incidents, improve safety performance, and foster a culture of continuous improvement. By identifying and addressing root causes, organizations can minimize risks, enhance safety awareness, and create safer work environments for employees.
By partnering with us for incident investigations and root cause analysis, organizations in Kenya can demonstrate their commitment to safety excellence, reduce the risk of workplace incidents, and protect the health and well-being of their employees.
Our ISO 45001:2015 implementation services in Kenya offer organizations comprehensive support in adopting and integrating occupational health and safety management systems (OHSMS) based on the ISO 45001 standard. ISO 45001 sets out requirements for establishing, implementing, maintaining, and continually improving an occupational health and safety management system to enhance workplace safety and reduce risks.
Our process begins with a detailed assessment of the organization’s current occupational health and safety practices, policies, and procedures to identify gaps and opportunities for improvement. We work closely with key stakeholders to develop a customized implementation plan tailored to the organization’s unique needs and objectives.
Throughout the implementation process, our experienced consultants provide guidance, training, and support to help organizations establish the necessary infrastructure, processes, and controls required by the ISO 45001 standard. This includes developing OHSMS documentation, defining roles and responsibilities, conducting risk assessments, and implementing performance monitoring and measurement systems.
We assist organizations in aligning their occupational health and safety management systems with ISO 45001 requirements, ensuring compliance with relevant regulations and industry best practices. Our goal is to help organizations create safer work environments, prevent work-related injuries and illnesses, and enhance overall occupational health and safety performance.
Upon successful implementation, we support organizations in preparing for ISO 45001 certification audits conducted by accredited certification bodies. We provide ongoing support to maintain compliance with the standard, address non-conformities, and drive continual improvement in occupational health and safety management practices.